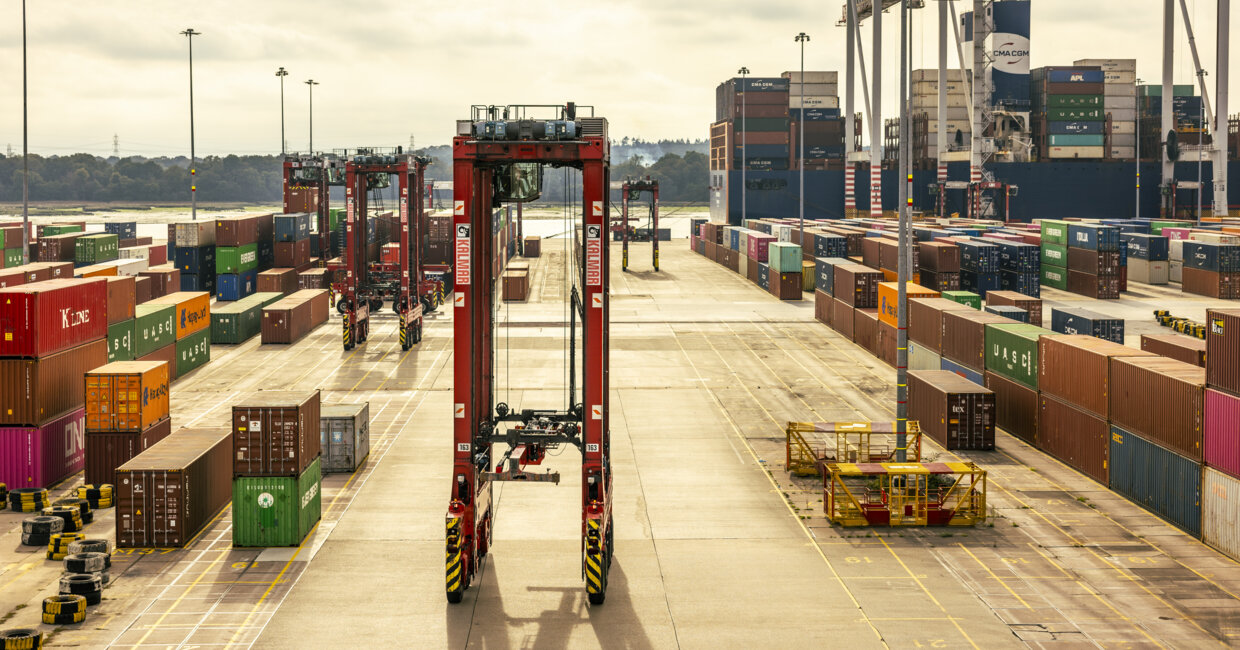
Kalmar Hybrid Straddle Carriers Dominating the Market
In the rush to decarbonise port and terminal operations, the quickest gains are made by switching from diesel to hybrid or fully electrified vehicles. In recent years, Kalmar Hybrid Straddle Carriers have proven wildly popular, accounting for more than 50% of straddle sales. Read on to discover how the company’s hybrid straddles are being used in today’s future-oriented ports and terminals.
For many decades, burning diesel has been a simple and effective way to power industrial equipment. But reducing emissions has become a significant concern for port and terminal operators. Corporate imperatives, the cost of fuel and stricter environmental legislation are forcing change in many jurisdictions.
Going electric is a great way to drastically reduce both local emissions and noise levels, but not all operators are able to transition to fully electric equipment. This is where the Kalmar Hybrid Straddle Carrier is playing an important role, as it provides an excellent alternative for operators who are not able to transition to fully electric equipment.
Hybrid straddle carriers account for over 50% of sales
“Since 2014 we have sold over 600 hybrid straddle carriers,” explains Aki Heikkinen, Sales Development Lead, AMEA at Kalmar. “Not only big global terminal operators are going in this direction; smaller local operators are also attracted by the competitive advantages of more eco-efficient operations, especially as customers focus on cleaning up the carbon intensity of their supply chains.”
On average, cargo handling equipment accounts for roughly one quarter of the total emissions at a container terminal. There are a host of ways to cut terminal emissions, from automation, energy regeneration and introducing hybrid or electric drivelines, to fleet-level solutions like route optimisation.
“But you have to go beyond the equipment itself and consider systems efficiency,” highlights Heikkinen. “How efficiently is your fleet utilised? How smart is your terminal operating system at minimising unproductive moves? Overall resource efficiency is a big piece of the puzzle.”
Kalmar Hybrid Straddle Carriers: efficiency in motion
Since launching its first straddle carrier more than 50 years ago, Kalmar has become a leading supplier of eco-efficient hybrid and fully electric transport solutions. Its vision for a hybrid straddle took shape back in 2008, resulting in a highly eco-efficient machine today. The hybrid straddles rolling off the production line now use up to 40% less fuel and cut CO2 emissions by as much as 50 tons per year compared to diesel-only equipment.
“Real fuel savings depend on a number of factors including driving distances, ambient temperature, terminal operating mode and so on, but our theoretical calculations have been backed up by real-world data from hundreds of machines in operation today,” says Heikkinen.
For operators looking to reduce their carbon footprint even further, switching to HVO (hydrotreated vegetable oil) fuel is a way to make a big impact. Kalmar Hybrid Straddle Carriers are HVO compatible, enabling up to 90% lower fuel emissions.
A case in point: long-time Kalmar customer DP World Southampton, aiming for net-zero emissions by 2040, has introduced both Hybrid Straddle Carriers and HVO fuel as a vital step towards reaching their target.
Kalmar Hybrid Straddle Carriers are HVO compatible, enabling up to 90% lower fuel emissions.
Easier maintenance and lower noise levels
“We know from experience that in a typical terminal, straddle carriers can idle up to 50% of the time,” explains Heikkinen. “The Kalmar Hybrid Straddle Carrier cuts diesel engine idling out completely, since the diesel engine only comes on when batteries require topping up.”
Li-ion batteries are coupled with a smaller, compact diesel unit that starts and stops as required to recharge the batteries. And as the straddle goes about its work, it converts energy from deceleration and spreader lowering into additional electrical power.
Straddle carrier batteries are housed in a modular power unit on the hybrid machine’s top frame, along with a battery cooling system and a hydraulic system that powers braking, steering and spreader movement. Battery modules maintained with Kalmar Hybrid Service have a lifetime of around 10 years. Over 2.5 million operating hours is evidence of the proven technology.
50% less cabin noise makes for a much more pleasant operator work environment
“The hybrid machines are not only much more efficient, but also quieter,” notes Heikkinen. “Outside sound is 6 decibels lower than diesel-only machines, while cabin noise is 50% reduced. That makes for a much more pleasant work environment for operators.”
Learn more about Kalmar Hybrid Straddle Carriers and Kalmar Electric Straddle Carriers.
Related articles
Further reading
Subscribe and receive updates in your email
Abonneer je voor onze publicaties