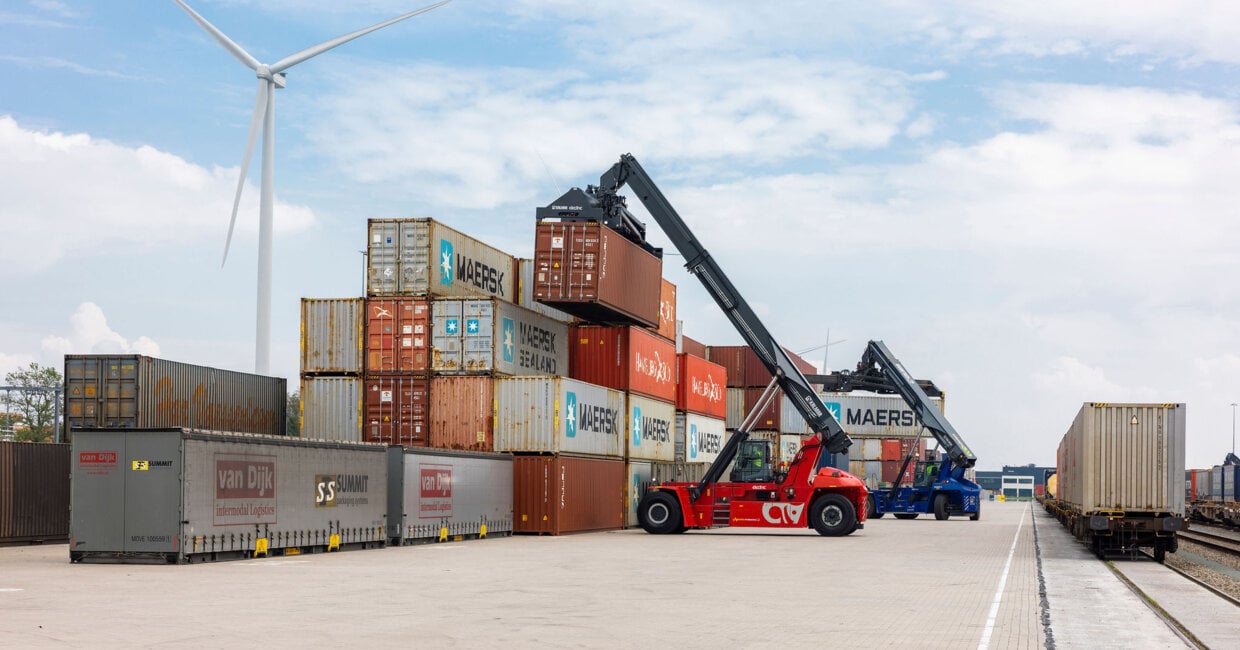
Part 2: Towards Carbon Neutral - Key takeaways from Green Chair LIVE
In Part 1 of this article, we learned some of the ways to grow your business while bringing emissions down. These include knowing the CO2 emissions of your business, including the impacts of upstream inputs and downstream product use. At Kalmar, sourcing steel structures and components constitute a significant CO2 input but with green steel we can significantly reduce our emissions.
But as we discover, planning with ecological impacts in mind needs to affect all aspects of the value chain. Part 2 of this article takes us further down the road towards carbon neutrality, starting with an explanation of how green technologies apply to the material handling industry.
Green technology
If steelmaking—one of the world’s most energy-intensive industrial processes—can go green, many other aspects of industry can as well. As Lasse Eriksson, Head of Green Technologies at Kalmar notes in the event, we are currently experiencing the biggest transformation since the industrial revolution when it comes to material handling. Most vehicle fleets still operate on diesel, but many alternative and greener technologies are emerging. The question is, can we do something now to reduce emissions, or should we wait for a future miracle?
Yes we can, and let's start with electric equipment. “Electrification is not the newest thing,” says Eriksson. “It has come through the whole Kalmar offering. The first Kalmar forklift trucks have been electric since the 1980s.” Battery-electric vehicles, like the electric heavy forklifts in operation at NorSea Norway, run full shifts without the need of frequent charging. They do, however, require the installation of charging infrastructure.
Eriksson outlines a number of alternatives for diesel on top of battery-electric vehicles:
- Biofuels - especially HVO100 is chemically similar to diesel, but it results in up to 90 percent lower CO2 emissions. It is, however, only available in a limited number of markets globally.
- Hybrid machines use a diesel engine to charge batteries that power an electric drivetrain. This creates significant fuel savings, typically approximately one third of diesel and thus emissions are saved. There are no changes to infrastructure required as diesel remains the sole source of power.
- Hydrogen - both internal combustion engines using hydrogen as well as hydrogen fuel cells are options for local low emissions, but green hydrogen only accounts for two per cent of hydrogen produced globally, with the remaining 98% generated using at least partially non-green sources of energy or production processes. Hydrogen fuel cells can provide more operating hours between fill-ups compared to a battery-electric vehicle, but converting electricity to hydrogen (i.e. hydrogen production) and then back to the electricity that powers motors in the machine, results in a poor overall efficiency. This means that we might end up consuming up to three times more energy in a fuel cell based operation compared to a battery-electric! New infrastructure is also needed as hydrogen is rarely available onsite.
It’s clear that battery-electric drivetrain is the best solution right now, both from a CO2 reduction perspective and for long-term financial benefit. It’s here, it’s a mature technology, it’s efficient, and the possible changes to machine operations required by charging breaks can be planned ahead in order to minimise the impact to the overall performance. Often the battery-electric machines can work the same shifts as diesel versions.
When an audience member asked how he foresaw digitalisation of Kalmar machines fostering green technology, Eriksson was enthusiastic. “There are so many opportunities to use data, analytics and AI to support machine and operational design in order to drive down the emissions,” he observes. “But it all comes back to data. First you need to know your operation, collect data on machine usage and fuel consumption, then do the modelling required to be certain that you are putting the right solution into place.”
The green transition
Battery-electric equipment is a clear winner at the moment, but there is no ‘one-size-fits-all’ solution. As Christopher Saavedra, Senior Manager, Terminal Design Services with Kalmar notes, there are lots of local deviations. “You have to consider that customers around the world have different initiatives, different levels of legislation, different manners of electricity generation,” he says. “The right solution for you depends on your specific targets and current situation.”
At the event, we received a question that touched on this global aspect: how do you ensure that the purchase of electrical hybrid equipment does not result in a transfer of emissions from one part of the world to another part. Eriksson suggested that you need to take into account the CO2 emissions of the electricity being sourced. Saavedra agrees and goes a step further, suggesting that the many different initiatives and levels of legislation around the world play into the decision-making process around specific environmental and financial targets.
To understand the challenges of designing a future-proof terminal, Saavedra engages Port of Aalborg experts Jesper Raakjær, Group Chief Visionary Officer, and Søren Bæk Christensen, Director of Operations, in conversation at the event. Saavedra explains the many ways in which they are managing their green port initiative. Without giving too much away, it’s fair to say that Raakjær and Christensen looked at the entire logistical chain—cargo companies, freight forwarders, Kalmar and other players, as well as carbon tax legislation—in designing the terminal.
Saavedra fielded a question about the length of time it takes to execute a complete terminal design project. “It depends on what the customer is looking for,” he said, “but typically five to six months, and we are lucky if there is no civil engineering work involved,” he smiles.
Saavedra notes that a transition to sustainable cargo handling needs to consider operational, financial and environmental components. In the case of a brownfield site transition, operational disruptions must be minimised. The transition should not increase costs or result in a lower ROI. And meeting environmental targets requires an investment plan matching the pace of decarbonisation.
When we asked our audience what they saw as the biggest challenge associated with the green transition, 26% thought it would be operational aspects and impact, 38% predicted that it would be financial aspects, 16% believed it would be technology challenges, and 20% thought that the biggest challenge in making the transition would be the resources required for handling it.
Putting targets into alignment
Kristoffer Kloch, former Innovation & Partnerships Project Manager at DFDS tells that DFDS, a company well known for moving goods and people since 1866, is unequivocal about being one of the big emitters in the industry and also its social responsibility to reduce its CO2 emissions. “Our customers are increasingly demanding solutions,” says Koch. “But it’s not just about compliance. It’s a business opportunity.”
The company’s ambitious strategy involves a 45 per cent reduction in sailing, driving, and terminal-operation emissions by 2030, and a transition to 100 per cent emissions-neutrality by 2050. DFDS is making quick headway. Besides electric equipment, the company is currently testing ammonia and hydrogen on some vehicles.
DFDS is making progress in other areas as well, such as installing windmills at terminals. Overall, the company has split emissions reduction into three innovation teams: Sustainable logistics, Sustainable fleet, and Collaboration (making smarter changes).
It was our great pleasure to discuss the decarbonisation of our industry together with SSAB, DFDS and Port of Aalborg. A big thank you also to our great audience for your interest and active participation! If you missed the event, you can watch the recording here.
Related articles
Subscribe and receive updates in your email
Abonneer je voor onze publicaties