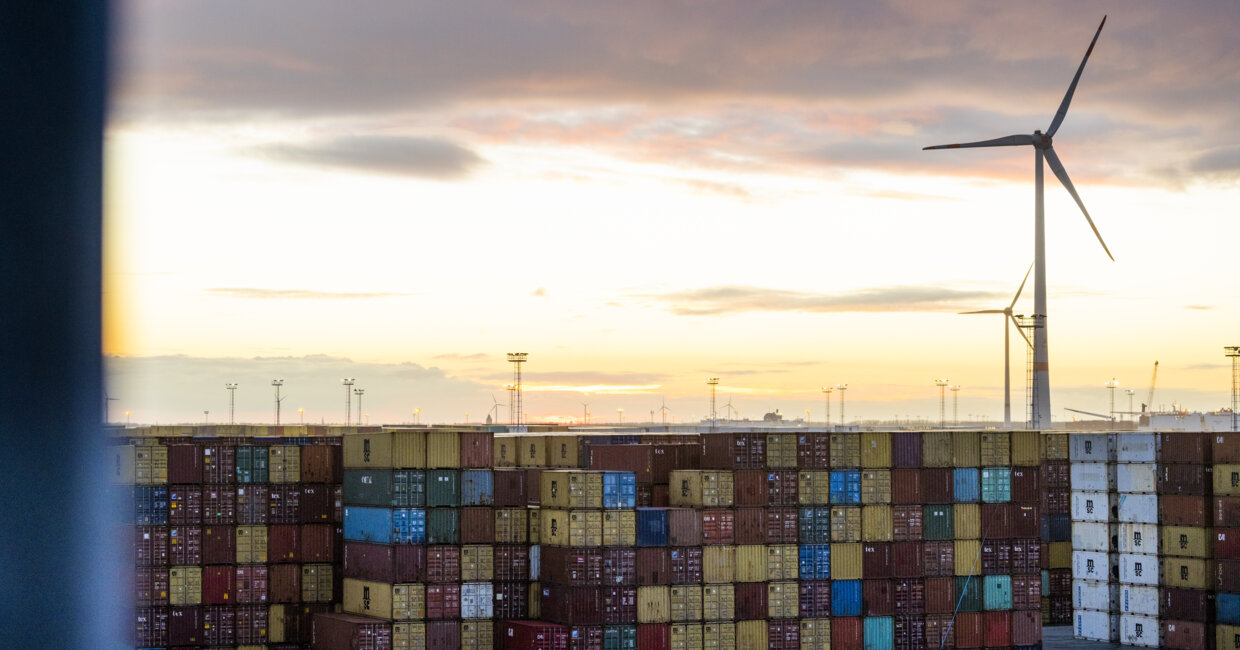
Part 1: Towards Carbon Neutral - Key takeaways from Green Chair LIVE
Former Norwegian Prime Minister Gro Harlem Brundtland defined sustainable development as “development that meets the needs of the present without compromising the ability of future generations to meet their own needs.”
As a leader in sustainable cargo handling, Kalmar is doing its utmost to push the industry in this direction. In the Green Chair LIVE online event, now available as an on-demand webinar, Kalmar experts and invited guests discussed ways for heavy industries to grow and prosper in a genuinely sustainable fashion.
Here are some of the many points that they make:
Grow your business, reduce emissions
“There is a way to grow your business while bringing emissions down,” says Mette Kjems Baerentzen, Head of Sustainability at Kalmar. “It’s got to do with buying and selling the right products.” From a climate perspective, the right products for Kalmar to sell are our eco portfolio solutions including hybrid and electric straddle carriers, eco reachstackers, electric forklifts and reachstackers, as well as circular service solutions. The eco portfolio is Kalmar’s most important tool to reduce CO2 emissions.
“But the green transition needs to go faster if we’re going to reach the Paris Agreement targets,” adds Baerentzen. “It takes 25 years to change a whole value chain. In 2023, we only have a few years left.” She believes that many initiatives all need to work together to achieve sustainability, starting with regulation and incentives. For instance, in the US, the Inflation Reduction Act of 2022 offers a $369 billion investment in the modernization of the American energy system. On the other hand, the EU’s Carbon Border Adjustment Mechanism (CBAM) will put a price on the carbon emitted during the production of carbon intensive goods that are entering the EU.
“If we work together to get both the push effect from the necessary compliance and the pull effect from commitment and governmental incentives, we can transform our industry into a new, sustainable format,” affirms Baerentzen.
Know your value chain CO2 emissions
Value chains hold the key to 90% of emission reductions, says Marjolein Koopman, Head of Sourcing Sustainability at Kalmar. However, when we asked our audience if they know their CO2 emissions, 38% said no, 21% said yes and 41% said partly. As poll results show, value chain emissions can be complex. But there are several ways to tackle this issue:
Our own operations account for less than 1% of our total emissions. Purchased goods upstream account for 16% and use of sold products downstream for 83%.
Calculating the entire carbon footprint is the key
By calculating our upstream emissions, we can uncover the emission hotspots in our supply chain, and actively implement different ways to reduce the emissions. At Kalmar, we are conducting life cycle assessments to understand all the stages of the life cycles of our equipment. We collect detailed information from our highest-emitting suppliers on, for example, energy usage and material sourcing, all the way down to raw material extraction, to get a full picture. We use this information in our emissions reporting to find emission hotspots and to reduce emissions together with suppliers in their operations.
“Disclosing your value chain carbon footprint is not only a matter of compliance; it is a way to earn the trust of your stakeholders and identify risks in all of your business’s upstream and downstream activities,” says Marjolein.
Kalmar’s carbon transparency is symbolic of our commitment – we have embedded emission reduction into our decision making, including supplier selection and RFP valuations.
Green steel solving the steel conundrum
However, with more than 1,000 suppliers and several hundreds of thousands different parts, it’s a challenge to manage upstream sustainability. At Kalmar six key sourcing categories (steel structures, power trains, castings & forgings, electrics, hydraulics & cylinders, tires & rims) represent 75% of our supply chain emissions, with steel structures being the biggest, at over 50% of our supply chain emissions. While emission-intensive, steel is also the most recycled material in the world—and quickly becoming even more so. Yet we use so much of it globally that we must solve the steel conundrum.
Who better to talk about reducing the carbon emissions of steel than Thomas Hörnfeldt, VP Sustainable Business at SSAB, the largest steel producer in Scandinavia? “Making steel from iron ore creates a lot of CO2 emissions so we cannot go on making steel as we have done since the 13th Century,” says Hörnfeldt.
SSAB’s HYBRIT technology is changing the way steel is made; it’s fossil-free. Creating a tonne of iron currently involves producing at least 1.5 tonnes of CO2. It’s part of the deal; it’s a chemical fact. But in Sweden and Finland, carbon-free power grids can use electrolysis to make ‘green’ hydrogen for ironmaking without CO2 emissions. Then the oxygen in the iron ore will move not to carbon to form CO2, but to hydrogen to form water. All the downstream processing—the alloying, the casting, the rolling, the heating and so on, will be done as today, but using fossil-free electricity. SSAB’s steel products will be at least as high-performing as they are today.
SSAB Zero is another example of how we can produce steel with zero emissions. It’s a steel product made entirely from recycled steel. In the U.S., fossil-free electricity and biogas are used to melt steel without CO2 emissions. The resulting steel slabs can be rolled into finished products at the U.S. plant, or put onto a biodiesel-powered ship for greenhouse gas free processing at SSAB plants in Sweden and Finland.
Kalmar is looking into increasing the recycled content of steel in its products. As a first step, Kalmar customers now have the option of having their electric reachstacker constructed partly with SSAB Zero™ steel made from recycled steel and produced using fossil-free electricity and biogas.
Eco-design puts precise focus on the environmental impact
Other tactics that we have started to put in place are rethinking packaging, using less surface treatment-intensive processes, and designing products and services from the ground up with special consideration for their environmental impacts over their entire life cycles, like we do with our eco-design process. As an example, we are transitioning counterweights from cast iron to natural materials, such as stone. We are moving to adopt the same materials, shapes and sizes for all equipment, which is more efficient, and strive for longer product life cycles.
Based on the event's poll results, there is a large variation in companies' biggest share of emissions. This shows how the distribution of emissions depends greatly on the type of business. In the next part of the article, we will discuss this more and cover an aspect which is playing a big role in the picture: green technology. In addition, we will introduce two customers who have been taking significant steps in their green transition and leading the way in the industry.
Related articles
Subscribe and receive updates in your email
Abonneer je voor onze publicaties