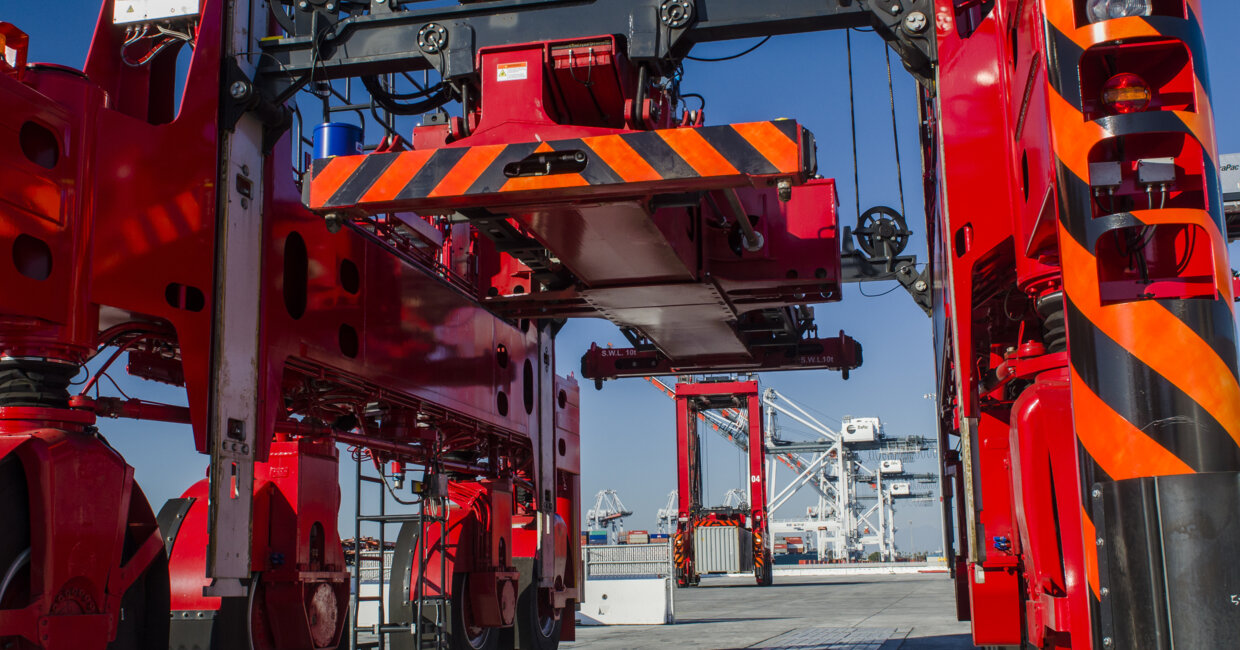
When you take care of your automated equipment, it will take care of you
Aside from the obvious difference of there being less or no onboard human involvement in operating the machinery, semi-automated and automated container terminals are also worlds apart in terms of the optimal approach to maintenance planning and execution. In this article, Kalmar’s leading experts in the field discuss the changes needed in practices and attitudes when adopting automation technologies from the point of view of a terminal’s maintenance, operations and IT teams.
For any container terminal, taking the step from manual to semi or fully automated operations represents a drastic difference in terms of the complexity of the operating environment. While we are still talking about mechanical solutions – stacking cranes, straddle and shuttle carriers, and RTGs for example – moving boxes around in a space, they are now doing so under the control of a complex, finely tuned automation system where servers and software are the nuts and bolts that hold everything together.
It is no surprise then, that at automated terminals IT shifts from being a separate department to a critical function that needs to work together seamlessly with the operations and maintenance teams.
“From the perspective of the maintenance philosophy, the most significant difference when adopting automation is that you have to move away from reactive ad hoc repairs and develop a targeted preventive maintenance programme focused on early intervention and root-cause analysis based on data gathered from the equipment,” explains Juhana Määttä, Senior Sales Manager, Kalmar Services.
Teemu Tapio, Senior Manager, Service Sales and Remote Support adds: "Automated terminals typically see longer component lifetimes in the steering system, powerline and spreader partly because of the strong focus on preventive maintenance. Additionally, automated machines are operated more smoothly by the terminal automation system rather than by humans; this combination is an excellent way to save energy consumption, extend component and machine lifetime.”
With no drivers onboard to report issues like unusual vibration or noises, repeated fault codes or other problems, the equipment control system is your eyes and ears on the ground, gathering vast amounts of valuable data that can be analysed to identify trends and plan preventive maintenance.
Keep your team in peak condition, or risk losing in the long run
Juhana uses the analogy of a football team to explain the differences between manual and automated terminal setups. “If we imagine 11 straddle carriers as our players, in a manual setup you can still field the ‘injured’ ones – perhaps with the odd oil leak or fault code – and get the job done. And if a machine breaks down, it can still limp back to the substitutes bench,” he explains.
“In an automated setup the equipment works best when faults are dealt with preventatively, because if there’s a problem the automation system will notice the faults and send it off for investigation. Keeping to a rigorous, systematic maintenance regime also helps to avoid unexpected breakdowns in challenging locations, which disrupt operations.”
With automated equipment there’s an extra layer of onboard maintenance to take into account beyond the traditional oil changes and other preventive maintenance activities associated with manual machines, as Juhana points out: “There are likely scanners, lasers and computers onboard, which are the machine’s eyes, ears and brains, and these need to be maintained too or you’re essentially sending the machine out blind, deaf and dumb.”
One point of contact means a better chance of success
Teemu continues by explaining that while choosing to forgo the time and effort needed to develop a solid preventive maintenance approach might save you money in the short term, it will cost you in the long run in the form of poor productivity and profitability.
“Forward planning for maintenance is absolutely vital in an automated operation. When problems are identified they need to be addressed immediately, and penny pinching is not an option unless you want to end up with a fleet of expensive assets that are unable to perform properly. For terminal operators, having maintenance planning, preventive and corrective actions, and troubleshooting taken care of by as few suppliers as possible provides a far better chance of success. With clear lines of communication between IT, operations and maintenance, it is faster to identify and fix the faults.”
In terminals that are adopting automation for the first time, working with a trusted partner smooths the way. “Many terminals can call on outside help from people with the necessary skills and experience to operate and maintain automated equipment and systems,” Teemu says. “For example, analysing a fleet’s performance and condition – an absolute necessity in an automated operation – is likely beyond the scope of a typical maintenance technician’s work.”
A partner like Kalmar can take care of both sides of the equation – optimising the performance and maintenance of the physical machines through a consistent, proactive, data-driven maintenance approach while also making sure that the automation system is running with all the right configurations and parameters.
Seamless integration of the ‘holy trinity’
With Kalmar’s remote services offering, terminal operators have 24/7 access to advanced analytics services and industry-leading expertise. “An automated terminal generates vast amounts of vital data, and analysing that data helps to optimise both the performance of the machines and the effectiveness of maintenance activities. With remote support, we provide terminal operators with a hotline to the OEM and assistance with data analytics too,” says Teemu.
“If something can’t be solved in the field, the people who designed the software and the hardware are just a phone call away,” he continues. “In an automated terminal the ‘holy trinity’ of maintenance, operations and IT functions needs to work together seamlessly. We can help by providing equipment maintenance expertise to support the customer’s maintenance department, software maintenance and support for the IT department and operations support services to the operations team.”
Read more about how a Kalmar Care service contract lets you focus on your operations while we make sure that the competencies and materials you need are always available.
Related articles
Further reading
Subscribe and receive updates in your email
Abonneer je voor onze publicaties