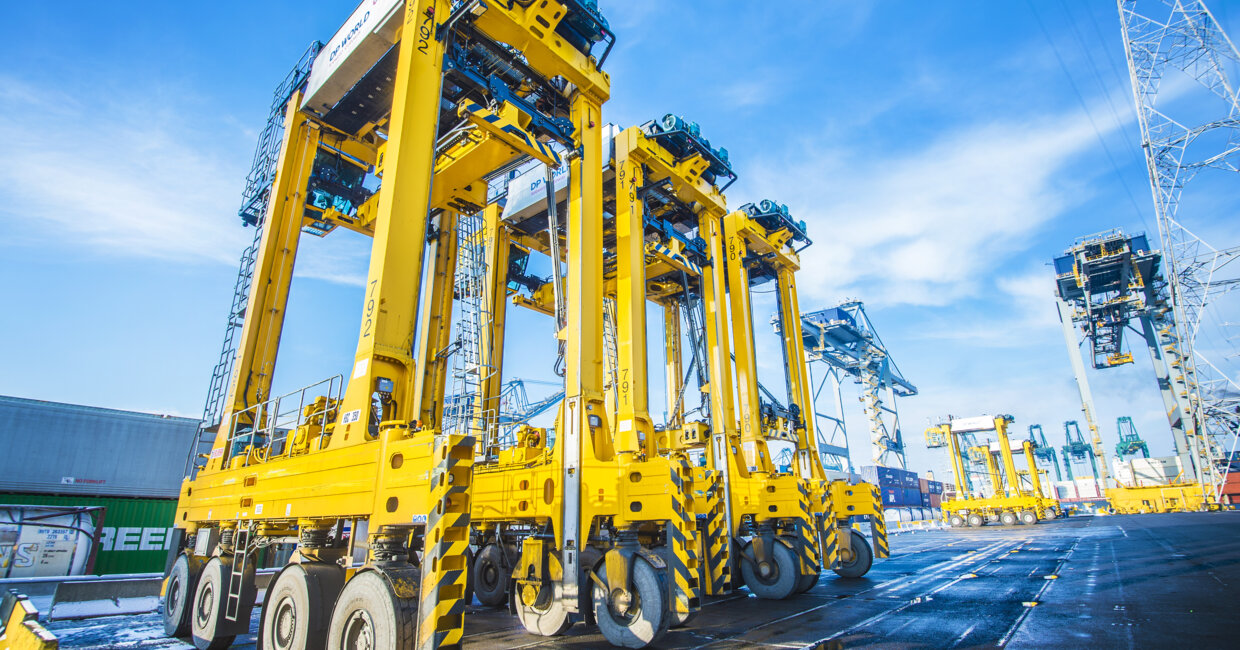
Carrying terminals towards a more eco-efficient future with hybrid straddles
Fifty years on from its introduction, the Kalmar straddle carrier is now a textbook example of what can be achieved with hybrid drivelines. Almost 300 hybrid versions have been ordered and delivered to date, including 43 to DP World Antwerp Gateway, and they are hard at work helping customers around the world to cut fuel costs, CO2 emissions and noise.
The Kalmar straddle carrier has benefited from plenty of significant technological advances over its long and distinguished 50-year history. There are now over 5,500 machines working in terminals across the globe, and in the future an increasingly large number of these will be hybrids – powered by the latest in lithium-ion (Li-ion) battery technology.
“While hybrid machinery is commonplace in our everyday lives now, back in 2008 when we began formulating our vision of a hybrid straddle carrier this was cutting-edge stuff,” says Mikko Nurmela, R&D Manager, Electrics at Kalmar. “We are lucky enough to have always had a talented and dedicated in-house team who keep their eyes on the prize, and once we decided that our focus should be on developing more eco-efficient solutions, we were off,” he continues. “What’s more, because we were designing everything in house we were able to ensure there are no compromises on safety.”
That meant some serious research and engineering work, looking at things like engine options, supercapacitors, flywheels and battery technologies to see what was available to create a feasible hybrid solution. The key was to identify the right battery technology that offered the required performance and capacity.
The Li-ions roar
In the modern Kalmar hybrid straddle and shuttle carriers the Li-ion batteries are combined with a compact diesel power unit, which is not only highly fuel-efficient, but also quieter and easier to maintain than the unit in a machine powered by diesel alone. They also feature a maintenance-free regenerative energy system that converts energy from deceleration and spreader lowering into electrical power, which is then stored in the battery system.
Eleven years ago, the Kalmar team was essentially starting from scratch. “We manufactured the first version of the hybrid straddle in 2009 using supercapacitors, and this was very much a learning process for us,” says Nurmela. “We were making mistakes and learning by doing, and we soon realised that batteries were the only way to go if we wanted to achieve the fuel-consumption reductions we were after,” he explains.
At the time there were no ready-made battery solutions available, so the team at Kalmar sourced battery modules from a variety of suppliers and built their own testing equipment and controls to evaluate them. “Learning by doing has been the key to enabling us to get to where we are today, by selecting components and designing systems that we can rely on and that deliver what we need,” Nurmela points out.
‘Where we are today’ is an eco-efficient solution that uses up to 40% less fuel and cuts CO2 emissions by as much as 50 tons per year compared to diesel-powered machines. “It’s not just about fuel and CO2 either,” Nurmela highlights. “Our hybrid machines are easier to maintain and use a lot less hydraulic oil: just 120 litres compared to 1,500 litres in a diesel-powered Kalmar straddle carrier. They also generate a lot less noise thanks to the smaller start-stop type diesel engine.”
DP World Antwerp Gateway goes hybrid
Kalmar and DP World, one of the world's leading operators of marine and inland terminals, have developed a highly successful partnership over many years of working together, and DP World’s Antwerp Gateway terminal is a shining example of what’s possible with hybrid straddle carrier technology.
The terminal took delivery of 19 Kalmar hybrid straddle carriers in October and November 2019, bringing the total number of hybrid units operating at Antwerp Gateway to 43.
“The environmentally friendly Kalmar machines will replace the old diesels in the long term. The hybrids further reduce CO2 emissions per container movement. Antwerp Gateway currently uses 7.5 kg CO2 per container unit (TEU). Our objective is to reduce CO2 emissions by 2% each year. Despite the extra cost, DP World consciously chooses this technology as a sustainable investment in the future. The partnership with Kalmar helps us to reduce our carbon footprint," says Suzanne Kwanten, HSSE Director at DP World Antwerp.
“We have come a long way since those tough but highly educational early years, and our decision to focus on hybrid back in 2008 has been validated. The fact that there are now over 300 hybrid straddle carriers working at all kinds of terminals around the world is something we’re really proud of,” Nurmela concludes.
Related articles
Further reading
Subscribe and receive updates in your email
Abonneer je voor onze publicaties